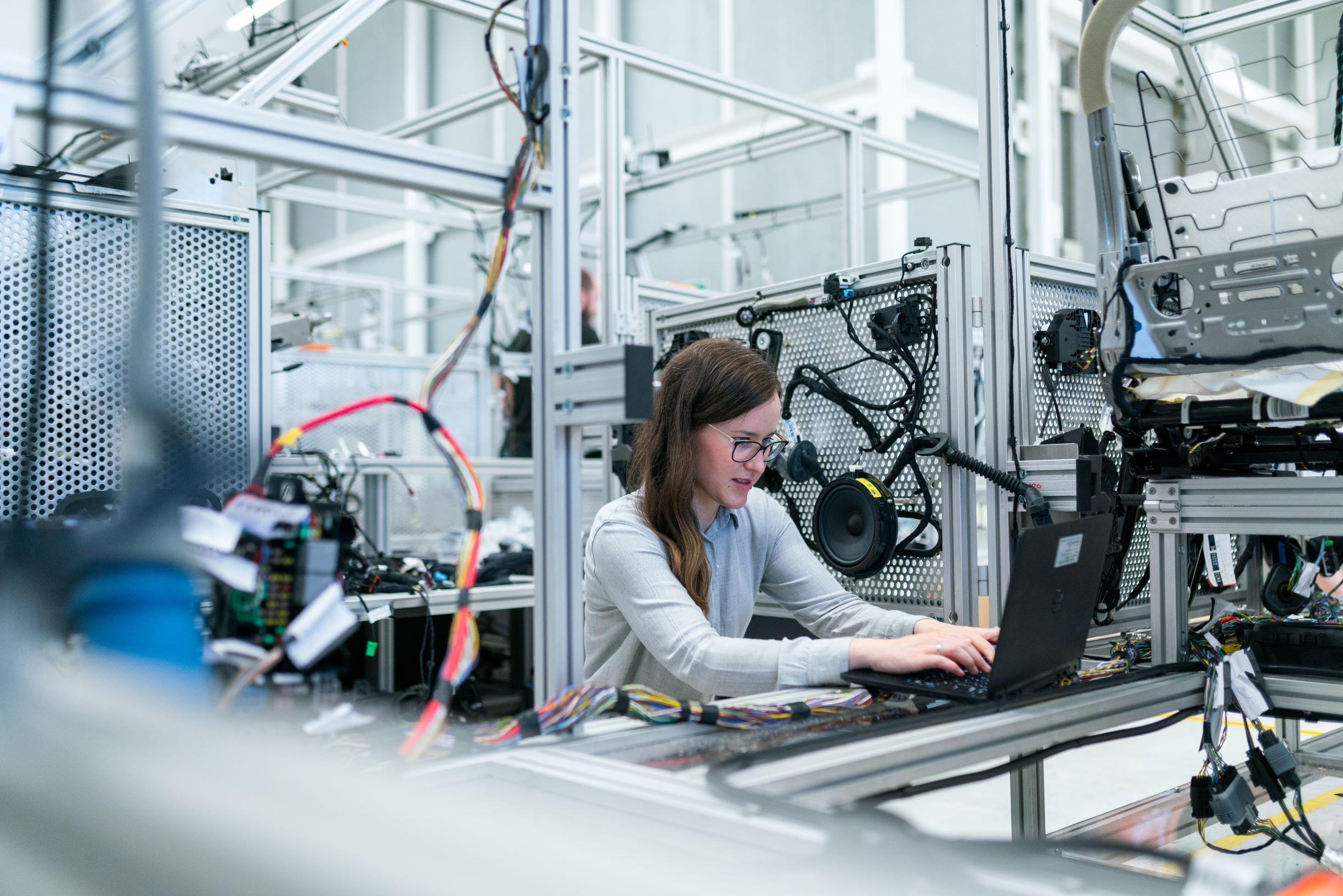
Digital Lean & Manufacturing Excellence
Modern Manufacturing Excellence
A recent study by Bain found that while traditional Lean produces a 15% reduction in operational costs, Digital Lean compounds this by 100% , for a total of 30% cost reduction. Digital Lean must now be considered as to how best to build into a companies Lean strategy to further enhance efficiencies and to exploit company growth opportunities.
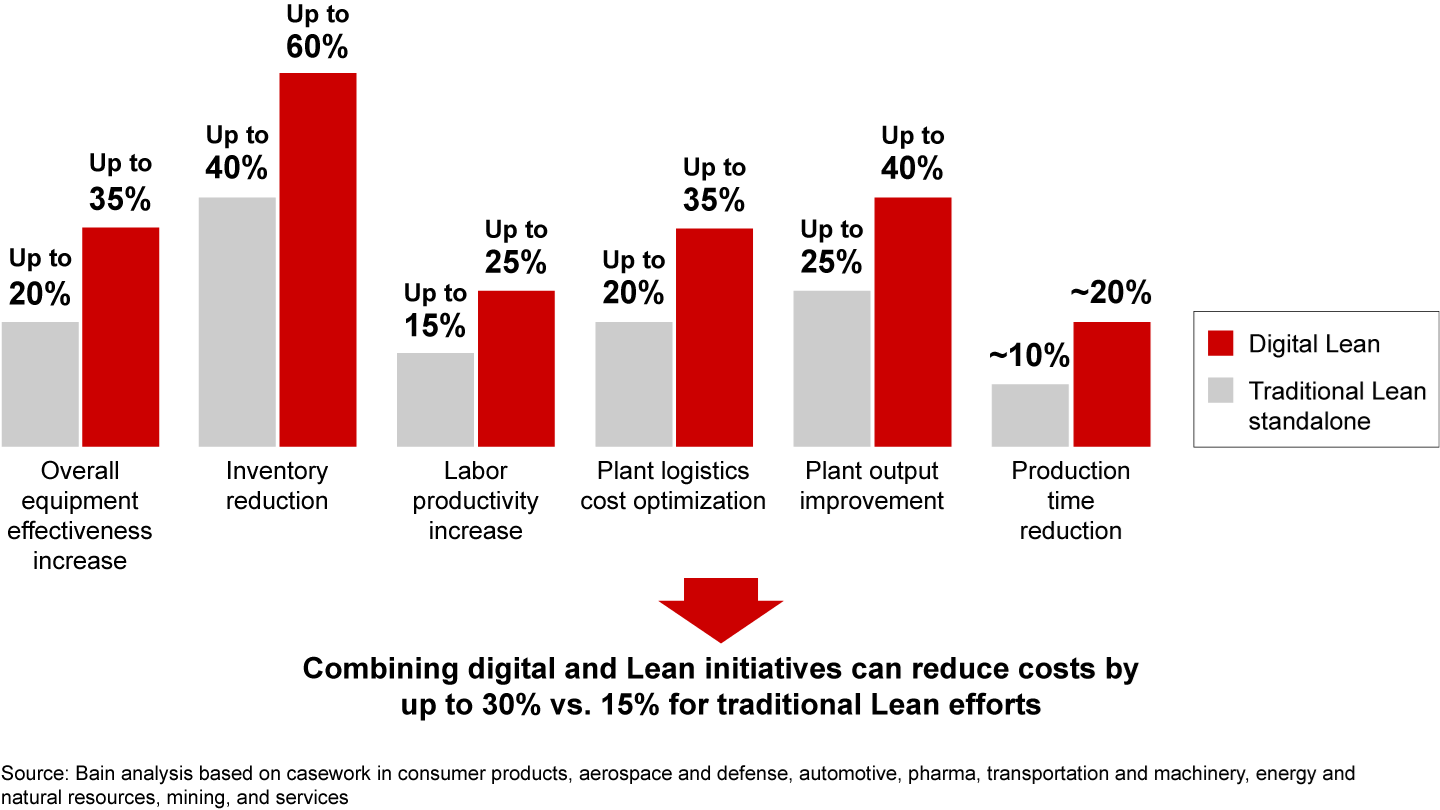
Across all industries, operations leaders are under pressure to embrace new digital technologies. There is a lot of literature that expands on the merits of “Industry 4.0” and “industrial IoT,” plus other evolving combinations of technology such as virtual/augmented/mixed reality with a plethora of other productivity based applications based on new digital technologies.
Like the recent exponential surge in data consumption, this new age of automation has brought exponential possibilities with associated challenges. At the core, industry knowledge and experience applied to a company’s operations remain central to understanding how best to apply Digital technologies to reap operational benefits.
There are four major technology trends that are redefining common industry competitive advantage. Three are digital enablers that are compounding the many benefits of Lean principles. Understanding these enablers is important to help steer a clear path towards “Digital Transformation.”
Four Technologies Transforming Manufacturing
Digital Lean is a movement that leverages data insights and key capabilities that continue evolve with technology progression.
Big data
Incredibly around 90% of the world’s data has been created in the last two years. The manufacturing shop floor is catching up and it has an enormous potential to gather very valuable data that may be converted into purposeful actions. Data gives managers a real-time view of production, processes, people, and equipment. This data may be used to exploit new opportunities in asset management, supply chain planning, resource allocation, and many other aspects of manufacturing. Data analytics and data modeling are now a necessity within Operations to create business insights and to ensure competitive operational practices.
Robotics
Robots capabilities, availability, and operational costs have dramatically improved over the last few years. Over the next three years, more than 1.7 million robots will be installed worldwide. Most of them will be "Cobots"; collaborative robots that are specifically designed to work with humans in a smarter way than previous generations of expensive robots. The economics are now difficult to ignore due to rising labor costs and falling robot prices.
Analytics
Analytics facilitates make-to-order manufacturing processes and nearly all other components of the manufacturing life cycle. There is now a need to ensure that analytics are fully integrated with other digital platforms, particularly manufacturing execution systems.
Internet of Things (IoT)
IoT capabilities continue to evolve. The many sensors relaying real-time data are now standard within predictive maintenance and warehouse management systems. IoT enabled equipment has the potential to enable self-maintenance and automatically notify staff when thresholds have been passed through pre-set alert conditions. IoT is a game changer for maintenance by allowing proactive activities that results in more uptime and reduced costs. In the warehouse, radiofrequency identification (RFID) tags provide precise real-time location and material status data. Hands-free wearables allow warehouse workers far more mobility eliminating double handling of large quantities of stock.
While we an an advocate of dreaming big, we are believers in starting with small Digial wins to build momentum. Talk to us today to find out how we may help with your Lean journey.
(For more information, reference the original article here.)